Injection Well Services – Class I Hazardous and Class I, II, III, V, and VI Non-Hazardous
Our personnel have hundreds of years of combined injection well experience and are familiar with state and federal regulators throughout the country. Petrotek offers engineering and geology services where licensed. On a continual basis, our staff provides technical consulting and field services regarding a wide variety of issues to ensure the continued safe and responsible operation of all classes of waste injection wells.
Team professionals provide technical services to operators of deep injection wells throughout the United States. Staff members have prepared underground injection control (UIC) permits and Land Ban Petitions that have been accepted by state and federal regulatory agencies; conducted reservoir modeling studies; and provided field activity supervision for facilities that require injection wells throughout the country. We have experience regarding all aspects of deepwells ranging from feasibility studies to design; installation; maintenance; testing and contract operations. Petrotek staff are experienced with deepwell permitting issues related to existing and new facilities throughout the United States including the Rocky Mountains, Mid-west, Plains and Gulf Coast.
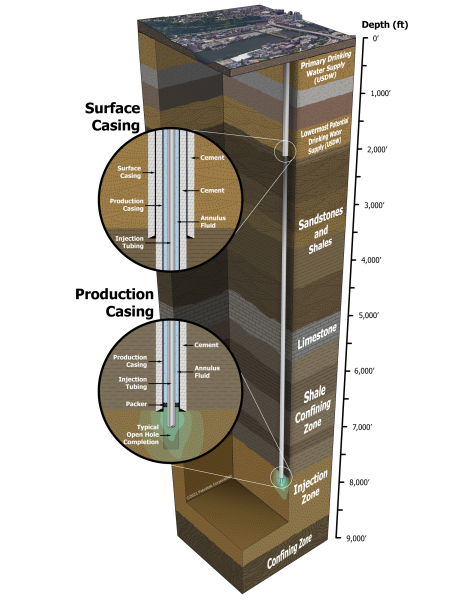
Permitting and Feasibility Studies
- Permitting for all well classes
- Fluid flow and transport modeling
- Aquifer exemption applications and regulatory support
- Geologic and reservoir evaluation
- Geospatial mapping
- Land-ban disposal exemption petitions
- Injection well regulatory negotiations
- Litigation support/expert witness testimony
- Well design, installation, completion and testing
Well Testing and Assessment
- Part I and Part II mechanical integrity testing
- Falloff/step-rate pressure transient testing and analysis
- Open and cased hole log evaluation
- Performance diagnostics
- Well feasibility and risk assessment
Field Operations
- Workovers, maintenance and repair
- Wellsite drilling and workover supervision
- Stimulation and completion optimization
- Wellsite project management
- Well closure (plugging and abandonment)
Operations and Regulatory Support
- Operations and compliance training
- State and Federal monitoring reports
- Compliance auditing and evaluation
- Contract injection operation
Learn more about Injection Well Technology
A wide variety of liquid wastes can be managed using deep injection well technology. Typically, these wastes are large water volume, low concentration waste streams that are aqueous and comprised of more than 95% water. Often these liquids have already been recycled or pre-treated and are not usable as a resource since they have little economic or energy value. Some common dilute wastes now managed via deep well disposal include:
- Salt Water Brines
- Dilute Hydrocarbons and Solvents
- Heavy Metal Solutions
- Agricultural Waste Waters
- Storm Water and Municipal Waste
- Meat & Crop Processing Liquids
- Inorganic Solutions from Manufacturing
- Industrial Cleaning Solutions
- Groundwater Clean-ups
For comparison, the concentrations of disposed materials in many of these injected wastes are similar to mixing a two-gallon can of a product like salt into a large tank of fresh water (2 gallons / 4000 gallons ~ 500 parts per million).
A wide variety of domestic and foreign facilities now depend on deep injection wells for the safe disposal of liquid wastes. Some of the industries in the United States that use deep injection well technology include:
- Food Processors
- Chemical Plants
- Oil and Gas
- Pharmaceuticals
- Ethanol Plants
- Cosmetics
- Municipal Water Supply
- Mining
- Refineries
- Power Generation
- Heavy Manufacturing
- Waste Management
- Potable Water-treatment
- Food Production
- Steel Mills
- Clothing Manufacturing
Disposal Well FYI
Disposal, or injection wells, are used throughout the world. In the United States, disposal wells associated with oil and gas production are regulated as Class II wells while industrial injectors are regulated as Class I wells. In the oil and gas industry, disposal wells can be found in most areas where hydrocarbons are produced. Class I wells are used in areas where there is an industrial need and where both restrictive geologic and hydrologic standards can be met. A primary consideration in well location is the natural ability of underground formations to contain and isolate both natural and injected fluids. The geology in many areas of the United States where a thick section of sedimentary rock is present often meet these strict requirements. There are more than 400,000 disposal wells currently operating throughout the United States. Approximately 1,000 of these injectors are Class I wells.
Class I industrial disposal wells are the safest, most effective way to manage many dilute liquid industrial wastes. Protection of drinking and irrigation water is the primary concern in the construction, operation and regulatory oversight of such wells. Deep well technology has been proven through wide use over more than 50 years. There has never been an instance of surface or drinking water contamination due to operation of a Class I disposal well that was sited, constructed and operated according to current US EPA standards.
- In the United States, Class I industrial deep wells are built to strict standards and operated under tight regulation and oversight. Class I wells have been used throughout the country during the past century to protect the environment from the surface disposal of industrial liquid wastes.
- Based on a number of academic studies and the collection of data from existing well sites, waste concentrations are reduced by natural processes in the disposal formation after injection. In addition to dilution by mixing with natural brines, neutralization, adsorption, precipitation, other reactions and microbial degradation occur in the injection zone. This serves as waste treatment underground.
- Disposal wells of various types are used in countries throughout the world to safely manage liquid waste by permanently isolating it from the environment. Environment Canada, the primary environmental regulatory agency in Canada, approves and permits disposal into deep wells in appropriate areas as a responsible option for the management of liquid wastes.
- The Kansas Department of Health and Environment says that “injection into a Class I well is considered an environmentally sound practice”. The state of Kansas has several hundred oil and gas disposal wells and almost 50 Class I industrial disposal wells.
- The Michigan Department of Natural Resources (MDNR) has documentation that no instances of contamination have occurred due to Class I well operation in the state. In addition, the Michigan Deep Well Injection Committee reported that “Most of Michigan has the subsurface geologic conditions required for proper waste disposal by deep well injection”.
- The largest concentration of disposal wells in the United States is in Texas (including almost 100 Class I wells). The Texas Commission on Environmental Quality that regulates these injection systems says that deep well injection has “an excellent record of environmental protection”.
Throughout the United States, the Environmental Protection Agency provides oversight and closely monitors deep well disposal operations under the Safe Drinking Water Act regulations. Laws, policies and regulations have matured over the past 100 years to enhance the safety of both non-hazardous and hazardous injection well operation. In many cases, state governments have been granted primary authority to conduct an Underground Injection Control (UIC) program. In others, the federal government directly implements the regulations. In all cases, strict standards are enforced by law to ensure that environmentally protective practices are followed. Geologic and engineering information is carefully evaluated and approved by regulators before deep well construction can begin and is reviewed after drilling has been completed, and before injection operations are authorized. Continuous protection of all usable groundwater is accomplished by rigid construction and monitoring requirements that provide at least four separate layers of protection. In addition to strict construction requirements, annual testing and limitation of waste type, disposal volume and injection well pressure are required to further promote protection of the subsurface environment. Detailed records of wastes disposed and all site operations must be submitted to the EPA or state regulators. Twenty-four-hour monitoring of operations is required to verify safe operation and permit compliance.
You can learn more about Class I injection wells by visiting the EPA website at: https://www.epa.gov/uic
By almost any definition, the naturally occurring waters typically present in injection zones are highly saline and unfit for use. The salinity of the native brines is often several times the concentration of normal seawater. In fact, the natural waters often demonstrate many similarities to some of the wastes that are injected into the zones for disposal.
Yes. The permitting process considers a wide variety of factors regarding injection well operations and site suitability which includes a determination of how long a well can be used and how much liquid can be disposed in a well. These limitations are determined based on the capacity of the disposal reservoir and the expected operational lifetime of the well components. Fortunately, these issues are also monitored on a daily, monthly and annual basis. If well monitoring shows any problems with system performance, the well must be shut down and repaired or permanently abandoned to make certain that waste stays in the injection zone according to the permitted well design. Clauses describing this monitoring, repair or abandonment, and the financial assurance to follow the specified procedures, are required as permit conditions before injection operations can begin.
Monitoring conducted to verify the suitability of the well for continued injection of waste is essentially of two types: continuous and periodic. Continuous monitoring provides data regarding how the well is operated, and is used to document operational changes that could signal any change in the well condition. Periodic monitoring is used to validate the continuous monitoring, and to more thoroughly investigate well and disposal reservoir conditions to verify waste containment.
Periodic mechanical integrity testing of well systems is conducted as required by regulations. Based on initial completion as a non-hazardous well, Part I annual testing may consist of standard annulus pressure testing and an associated reservoir falloff test. The annulus pressure test measurements are recorded using a calibrated pressure gauge on the wellhead, and are often witnessed by a regulatory inspector. A maximum change in pressure is allowed during the one-hour test. The gauges used to monitor pressure during the casing/tubing annular pressure tests are calibrated with a deadweight tester which is accurate to 0.1% of indicated pressure. Copies of gauge certifications are included with the pressure test records and reports.
Part II periodic mechanical integrity testing is completed before wells become operational and thereafter on a five-year cycle or as required by permit. For wells used to inject non-hazardous waste, this testing consists of a radioactive tracer survey or equivalent acceptable method to verify the adequacy of the cement at the base of the long-string casing. In addition, well logging designed to investigate vertical movement of fluids behind pipe will be conducted in the form of temperature, noise, oxygen activation logging or equivalent acceptable testing. Part II periodic mechanical integrity testing is required on an annual basis for wells used to dispose of hazardous wastes. Continuous monitoring of infection rate and other parameters will also be accomplished as required by regulation. Analysis of the waste stream for chemical and physical parameters is also completed on a case-by-case basis as required by permit.